Echometer Ultrasonic Bolt Load Measurement
The Echometer ultrasonically measures the elongation, stress and load in fasteners, quickly and accurately, and displays the result on an easy to read screen.
The measurement is achieved by determining the change in the transit time of an ultrasonic shock wave along the length of the fastener as the fastener is tightened.
The unit works with all bolt tightening systems and is used to monitor the fastener during the tightening process to ensure accurate initial loading. The retained load in the fastener can then be monitored at any time.
Echometer minimises the requirement for extensive operator training. With built in data recording and reporting through a RS232 interface, the echometer is quick and easy to use and offers a reliable solution to the most difficult bolting problem.
Benefits
- Quick and simple to operate
- Compact and durable for proven reliability
- Minimal operator training required
- Provides elongation, load, stress and strain measurements
- Accurate and reliable
- Designed to complement Boltight bolt tensioning equipment
- Easy measure during tightening and monitoring during plant operation
- Cost effective
- Simple data recording and reporting
- Most commonly used as load validation method.
- When torqueing a joint the coefficient of friction cannot be accurately known.
- Echometer acts as an independent check on correct joint tightening.
- In service monitoring – commonly with wind turbines.
- When the original bolt load is unknown – the Echometer can be used “backwards” to determine the load that was removed from the bolt.
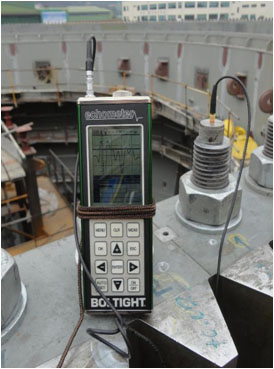
- Echometer is fast and easy to use.
- It gives accurate results
- It provides a permanent electronic record of bolting data
- Can be used to measure difficult to access bolts
- The Echometer can convert the data into load, stress or strain
- Programable with alarms to indicate that desired stretch has been achieved or too much has been achieved

- The size and frequency of the transducer is important
- Transducer sizes are specified based on the crystal diameter
- Choice of frequency will vary depending on material and bolt length
- Lower frequencies travel further whereas higher frequencies give a better resolution
- Temperature changes both the physical length and the ultrasonic length of a bolt
- These change at different rates to each other
- The variation in rate change is what limits the operating temperature to ambient
- Temperature probes are recommended when considering in-service monitoring
